
An acrylic box frame (BF) was fabricated using auto polymerizing acrylic resin.

Specially designed metal stand used in this study ensured same orientation of custom acrylic tray over metal die (fixed over the metal cube) and also maintained a uniform space of 3 mm between the metal die and the inner surface of the custom acrylic tray and also the same load was applied while making all alginate impressions. The space of 3 mm between the tissue surface of the die and custom acrylic tray and 1mm diameter of perforations with 1cm spacing between two perforations were followed as per the ADA specifications for the use of alginate material to avoid any influence on dimensional accuracy of the impression and thereby on the cast obtained by pouring the impressions. The perforations were then drilled all over using round stainless steel bur having 1 mm diameter and at a distance of about 1 cm from each other. After deflasking, a space of 3 mm all over was thus maintained to accommodate alginate mix of proper consistency. Flasking of this cast along with wax pattern was done in varsity flask using plaster mix following conventional method. A baseplate wax spacer of 3 mm thickness was adapted as per the outline marked over the cast, then the cast was duplicated using alginate material to obtain a duplicate master stone cast, over which the custom acrylic tray was fabricated. A stone master cast (MC) obtained by duplicating the metal die. This helped in maintaining uniform space of 3 mm between the metal die and custom acrylic tray to provide uniform thickness of the alginate impression material everywhere, as alginate is a ‘bulk’ impression material.Ī special impression tray was fabricated in heat cure acrylic resin. ‘V’ shaped notches were made at the horizontal land of the cast to facilitate proper orientation of the custom made acrylic tray while making impression each time.
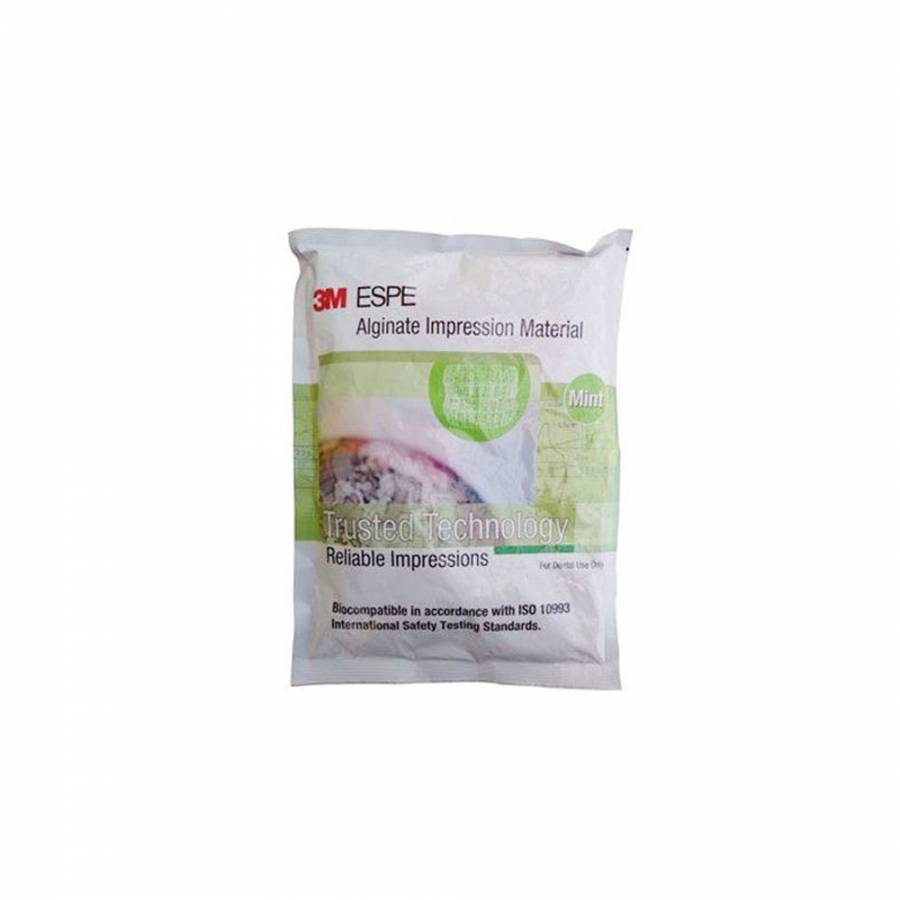

This modified stone cast was then viewed under travelling microscope for clarity of vision of selected points for ease of recording of distance between these selected points. Markings were done on mesiobuccal cusp tip of right first molar, cusp tip of right canine, mesioincisal angle of left central incisor, buccal cusp tip of first left premolar, distobuccal cusp tip of left second molar. Standard maxillary dentulous stone cast was used. analuminium die was specially prepared for this study. Nickel-Chromium plated Aluminium (metal) die, custom made perforated acrylic impression tray, metal stand with handle and platform, custom made acrylic Box frame for pouring cast. Travelling microscope (INCO, Ambala, Haryana India). A custom made apparatus was designed to maintain standardization and ease for impression making. Instruments & Equipments used in this study were Vernier calliper, Alginator (Algimax-II Holy medical Ltd), Humidor, Electrical balance (Aiwa, India Ltd), Vaccum mixer (Cuumyx confident), Room heater (Lazer quality appliances, India), Custom made Nickel-Chromium plated Aluminium die, perforated acrylic impression tray, acrylic Box frame for pouring cast.
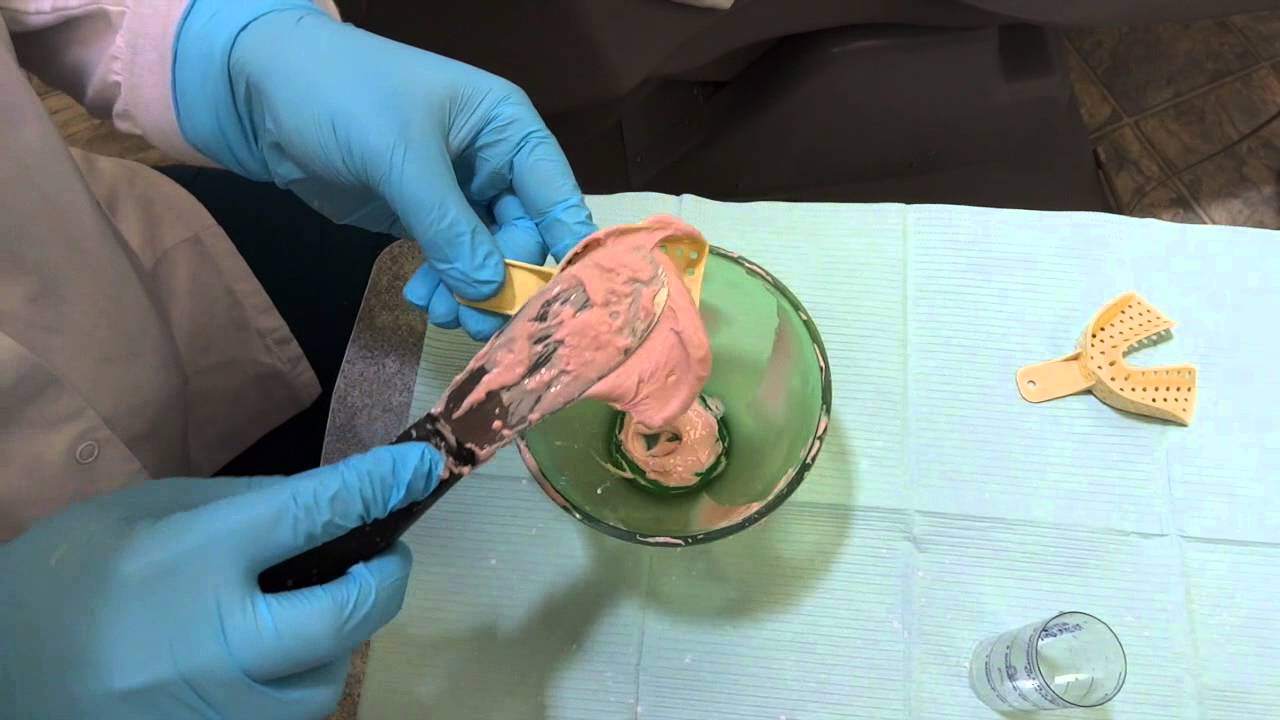
Maharashtra, India during 2009-2010 to evaluate dimensional accuracy of irreversible hydrocolloid (alginate) impression material by pouring impressions with variations in time of pouring and temperature.Ī-Velplast (Keller laboratories), B-Marieflex (Dentsply Ltd.), C-Zelgan (Dental Product of India), Gypsum Type IV die material Kalrock (Kalabhai manufacturers, Mumbai) & Heat cure acrylic resin (Dental Product Of India Ltd) were used in the study. The study was designed and conducted in the Department of Prosthodontics, Crown and Bridge Sharad Pawar Dental College, Wardha. Because of these facts, the present study was planned to evaluate the dimensional accuracy of different brands of Alginate impressions available in Indian market and provide insights for best possible time of pour to prevent distortion of commercially available impression materials. However, it begins to distort with the storage time for more than ten minutes and it cannot be used for clinical procedure like crown and bridge preparation after one to three hours. Alginate is used as a major dental impression material worldwide in many clinical procedures. Thus, considerable delay is caused in pouring the model, after removal of the impression from the mouth which is one of the reasons for causing dimensional changes in the impression, there by threatening the dimensional accuracy of the prosthesis. Because of time constraint pouring of impression by dentists themselves is on decline, as they prefer to send impressions to dental laboratories for making cast. Obtaining an accurate cast of a dental arch is an important step in the success of various dental treatments. Fabrication of successful and accurate prosthesis requires judicious application of experience and knowledge of dental materials.
